Unlocking the Potential of Aluminum Casting: Proven Techniques for Success
Light weight aluminum casting has long been acknowledged for its convenience and widespread applications across different sectors. Join us as we explore the vital aspects that can thrust aluminum casting towards unequaled success in today's competitive market landscape.
Advantages of Aluminum Casting
One of the primary advantages of light weight aluminum casting is its lightweight nature, which adds to fuel effectiveness in industries such as auto and aerospace. In addition, light weight aluminum is highly malleable, allowing for elaborate and complex shapes to be conveniently generated with casting processes.
Moreover, light weight aluminum casting gives superb rust resistance, making it perfect for applications where direct exposure to rough atmospheres is an issue. The product likewise shows great thermal conductivity, which is advantageous for markets requiring warmth dissipation, such as electronics (about aluminum casting). Furthermore, light weight aluminum is completely recyclable, straightening with the growing focus on lasting practices in contemporary production.
Layout Considerations for Casting
When considering casting layout, meticulous attention to information is paramount to guarantee the effective production of top notch components. The style phase plays a crucial function in the total success of an aluminum spreading task. One essential factor to consider is the choice of ideal geometries and features that assist in the spreading process. Designers need to consider elements such as draft angles, fillets, and wall thickness to make sure correct metal flow and solidification during casting.
Additionally, considerations connected to parting lines, gating systems, and risers are necessary to prevent issues like porosity and contraction. It is critical to maximize the style for effective product use and minimize post-processing requirements. Simulations and prototyping can be valuable devices in fine-tuning the casting and evaluating design before full-blown manufacturing.
Collaboration between style shops, manufacturers, and designers is essential to deal with any possible obstacles early in the style phase. By including these factors to consider into the spreading style procedure, manufacturers can improve product quality, reduce expenses, and eventually open the complete potential of aluminum casting.
Enhancing Casting Effectiveness
Creating with an emphasis on optimizing product circulation and minimizing flaws is necessary when intending to enhance casting performance in light weight aluminum casting projects. To attain this, utilizing simulation software program can assist in identifying prospective problems prior to the spreading procedure begins. By imitating the flow of molten aluminum, developers can readjust gating and riser styles to ensure proper dental filling and solidification, eventually minimizing the occurrence of problems such as porosity or shrinkage.
Moreover, executing appropriate warm therapy procedures can enhance the overall casting efficiency. Warm therapy can aid boost the mechanical buildings of the aluminum casting, guaranteeing that the final component meets the required specs. Furthermore, utilizing automation and robotics in the casting process can improve production, lower manual work, and increase total performance.
Furthermore, continuous surveillance and top quality control throughout the spreading process are critical for recognizing any discrepancies and making certain that the end products fulfill the wanted requirements. By executing these techniques, producers can enhance casting efficiency, boost item top quality, and inevitably right here accomplish higher success in aluminum spreading jobs.
Quality Control in Aluminum Casting
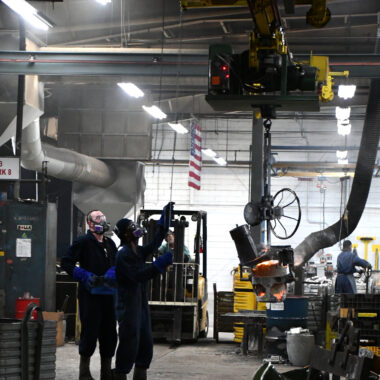
Effective top quality control techniques play a pivotal role in making sure the accuracy and reliability of aluminum casting procedures. Quality assurance measures in aluminum casting include a variety of activities targeted at promoting specific standards and determining variances that might endanger the end product. These practices begin with the careful selection and evaluation of basic materials to ensure their high quality and viability for the casting process. Monitoring and controlling the parameters of the casting process itself, such as pressure, cooling, and temperature rates, are important action in preserving consistency and stability in the final products.
In addition to procedure control, top helpful resources quality control in aluminum casting includes extensive screening and examination procedures at numerous stages of production. By executing robust top quality control techniques, light weight aluminum casting centers can supply items that meet client assumptions for efficiency, quality, and reliability.
Taking Full Advantage Of Productivity
To achieve optimum monetary performance, a thorough method for optimizing productivity within light weight aluminum casting procedures need to be meticulously designed and carried out. One key facet of taking full advantage of earnings in aluminum spreading is optimizing manufacturing efficiency.

In addition, expanding item offerings and checking out new markets can help expand earnings streams. Recognizing client demands and market fads can lead calculated decisions to capitalize on arising possibilities. Buying r & d to introduce procedures or products can additionally drive earnings with differentiation and consumer fulfillment.
Final Thought
In conclusion, light weight aluminum casting offers many advantages in regards to style flexibility, cost-effectiveness, and sturdiness. By carefully taking into consideration design considerations, improving casting performance, executing quality company website assurance measures, and making the most of success, producers can open the full capacity of light weight aluminum casting. This dependable and functional process has verified to be an effective choice for a variety of industrial applications.
Furthermore, aluminum is very malleable, allowing for intricate and intricate shapes to be quickly created via casting procedures.Reliable top quality control practices play a critical function in making sure the accuracy and integrity of light weight aluminum casting procedures.In enhancement to procedure control, top quality control in light weight aluminum spreading entails strenuous screening and inspection procedures at numerous phases of manufacturing. By implementing durable top quality control techniques, light weight aluminum spreading centers can supply items that satisfy customer expectations for reliability, high quality, and performance.
By very carefully taking into consideration design factors to consider, boosting casting performance, carrying out top quality control steps, and taking full advantage of profitability, makers can open the complete capacity of aluminum casting.
Comments on “Unraveling About Aluminum Casting: From Essentials to Knowledge”